Coating Thickness Measurement Gages
Coating thickness, paint thickness, or dry film thickness (DFT) is an important variable that plays a role in product quality, process control, and cost control. Measurement of film thickness can be accomplished by selecting the best mil gage for the particular application.
Why Dry Film Thickness Measurement is Important
Dry film thickness (DFT) or coating thickness is arguably the single most important measurement made during the application and inspection of protective coatings. Coatings are designed to perform their intended function when applied within the DFT range as specified by the manufacturer. Correct paint thickness ensures optimum product performance. Even the most basic specification will require DFT to be measured.
The Measure of Quality
Regular film thickness measurement helps control material costs, manage application efficiency, maintain finish quality, and ensure compliance with contract specifications. Paint manufacturers recommend target ranges to achieve optimum performance characteristics and clients expect these parameters to be met.
PosiTector 6000
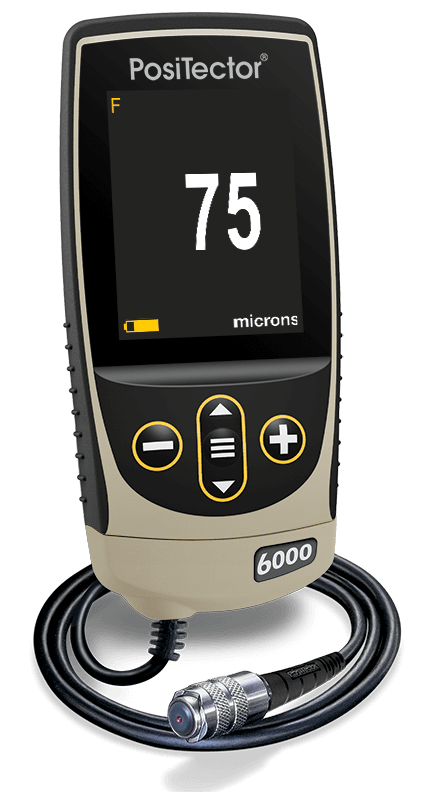
The rugged, fully electronic PosiTector 6000 Coating Thickness Gage uses magnetic and eddy current principles to measure coating thickness on both ferrous and non-ferrous metals, accurately and quickly.
PosiTector 200
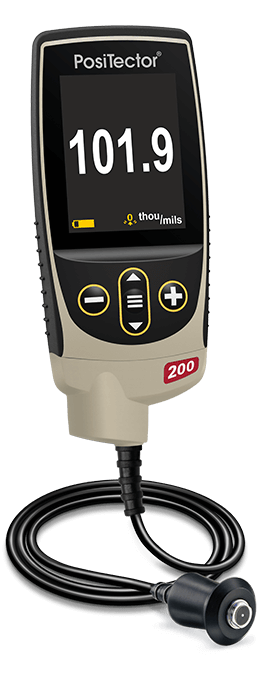
The PosiTector 200 Ultrasonic Coating Thickness gage non-destructively measures a wide variety of applications using proven ultrasound technology. Measure paint and coating thickness over wood, concrete, plastic, and more. Advanced models measure up to 3 layers with graphics.
PosiTest PC
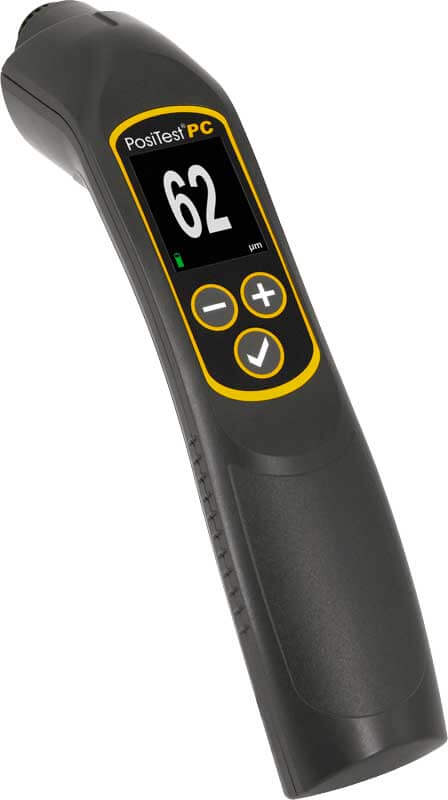
The PosiTest PC Powder Checker affordably measures uncured powder coatings using non-contact ultrasonic technology to predict a cured thickness.
Conforms to ASTM D7378.
Principles of Operation of Paint Thickness Gages
What are the types of Paint Thickness Gages available?
DeFelsko offers a variety of paint meters and probes for a wide range of applications including for measuring paint and coatings on metals, non-metals (wood, concrete, plastic, composites), and for measuring uncured powder coating thickness.
Check out our selection of paint thickness meters below.
What are Magnetic Film Thickness Gages?
Magnetic film gages (paint depth gauges) are used to nondestructively measure the thickness of a nonmagnetic coating on ferrous substrates. Most coatings on steel and iron are measured this way. Magnetic paint mil gages use one of two principles of operation: magnetic pull-off or magnetic/electromagnetic induction.
Magnetic Pull-off (Type 1 - Pull Off Coating Thickness Gages)
Magnetic pull-off gages use a permanent magnet, a calibrated spring, and a graduated scale. The attraction between the magnet and magnetic steel pulls the two together.
In Type 1 pull-off (PosiTest or PosiPen) gages, a permanent magnet is brought into direct contact with the coated surface. The force necessary to pull the magnet from the surface is measured and interpreted as the coating thickness value on a scale or display on the gage. The magnetic force holding the magnet to the surface varies inversely as a non-linear function of the distance between magnet and steel, i.e., the thickness of the dry coating. Less force is required to remove the magnet from a thick coating.
Magnetic and Electromagnetic Induction (Type 2 - Electronic Coating Thickness Gages)
Magnetic induction instruments use a permanent magnet as the source of the magnetic field. A Hall-effect generator or magneto-resistor is used to sense the magnetic flux density at a pole of the magnet. Electromagnetic induction instruments use an alternating magnetic field. A soft, ferromagnetic rod wound with a coil of fine wire is used to produce a magnetic field. A second coil of wire is used to detect changes in magnetic flux.
These electronic instruments measure the change in magnetic flux density at the surface of a magnetic probe as it nears a steel surface. The magnitude of the flux density at the probe surface is directly related to the distance from the steel substrate. By measuring flux density the paint thickness can be determined.
A Type 2 electronic coating thickness gage (PosiTector 6000/PosiTest DFT) uses electronic circuitry to convert a reference signal into coating thickness. Electronic ferrous paint thickness meters operate on two different magnetic principles. Some use a permanent magnet that when brought near steel, increases the magnetic flux density at the pole face of the magnet. Coating thickness is determined by measuring this change in flux density, which varies inversely to the distance between the magnet and the steel substrate. Hall elements and magnet resistance elements positioned at the pole face are the most common ways this change in magnetic flux density is measured. However, the response of these elements is temperature dependent, so temperature compensation is required.
Other ferrous electronic paint thickness gages operate on the principle of electromagnetic induction. A coil containing a soft iron rod is energized with an AC current thereby producing a changing magnetic field at the probe. As with a permanent magnet, the magnetic flux density within the rod increases when the probe is brought near the steel substrate. This change is detected by a second coil. The output of the second coil is related to the coating thickness. These paint meters also need temperature compensation due to the temperature dependence of the coil parameters.
What are Eddy Current Film Thickness Gages? (Type 2 - Electronic Coating Thickness Gages)
Eddy current techniques are used to nondestructively measure the thickness of nonconductive coatings on nonferrous metal substrates. A coil of fine wire conducting a high-frequency alternating current (above 1 MHz) is used to set up an alternating magnetic field at the surfac of the instrument's probe. When the probe is brought near a conductive surface, the alternating magnetic field will set up eddy currents on thesurface. The substrate characteristics and the distance of the probe from the substrate (the thickness) affect the magnitude of the eddycurrents. The eddy currents create their own opposing electromagnetic field that can be sensed by the exciting coil or a second, adjacent coil.
For instruction manuals, application notes, and technical articles for coating thickness measurement gages for all metal substrates, please find the following links:
How do you measure coating thickness on non-metals?
The ultrasonic pulse-echo technique is used to measure the thickness of paint and other coatings on non-metal substrates (plastic, wood, concrete, and composites) without damaging the coating.
Ultrasonic coating thickness gages (e.g. PosiTector 200) emit a high frequency sound pulse that travels into the coating via a coupling gel and reflects from ANY surface that is different in density. Paint thickness readings are obtained by measuring the time taken for the ultrasonic signal to propagate from the probe to the coating/substrate interface and back. The travel time is divided by two and multiplied by the velocity of sound in the coating to obtain the thickness of the coating.The PosiTector 200 interprets the largest "echo" within the selected range as the coating/coating or coating/substrate echo.
Coating Thickness Gage for Uncured Powder Coating Thickness
PosiTest PC Powder Checker — Non-contact Uncured Powder Thickness Gage
How do you measure Powder Coating Thickness before and after curing?
Thickness measurements of powder can be taken before and after curing. Substrate type, thickness range, part shape, and economics determine the best method to be employed.
For uncured applied powders, height measurement can be performed with DeFelsko Powder Combs. This technique is destructive and may require recoating the part. Coating powders generally diminish in thickness during the curing process so these procedures require a reduction factor be determined to predict cured film thickness.
Non-contact ultrasonic instruments, such as the PosiTest PC Powder Checker also measure uncured powder, but do so without touching the surface. Instead of measuring powder height, they automatically display a predicted cured thickness result. Accurate measurement at the time of application: eliminates over usage, improves quality, controls set-up, reduces rework & waste — saving money.
For after-cure measurement, a variety of hand held paint meters are available. These non-destructive instruments employ either magnetic, eddy current, or ultrasonic principles depending on the substrate.